Introducing EYE+ XTD
Robot guidance made simple and efficient
EYE+ XTD brings a new level of flexibility to robotic part localization. Powered by advanced AI algorithms, it provides accurate part coordinates—whether parts are placed on conveyors, in thermoformed trays, or on complex surfaces. From cable connection to first part pick, the intuitive interface guides you step by step—accelerating deployment and boosting productivity in demanding automation environments.
Built for part detection—ready to deliver robot coordinates
✔︎ User experience dedicated for easy part detection
Request part coordinates—EYE+ XTD takes care of the rest, delivering pick-ready robot positions in just a few hundred milliseconds.
Its intuitive user interface (UI) allows end users to configure new parts quickly and confidently, without needing advanced vision knowledge.
✔︎ AI-powered software
Carefully selected algorithms, fully integrated—offering simplicity, efficiency, and flexibility right out of the box.
✔︎ Simplicity
No vision expertise required. The intuitive web interface makes part localization fast and reliable—for both beginners and pros.
✔︎ Get coordinates in the right robot frame and format
Built-in hand-eye calibration ensures each part’s position is returned directly in the robot’s reference frame.
With a wide range of plugins, EYE+ XTD makes integration easy and communication with your robot seamless.
✔︎ Inspired by the Cyber Resilience Act (CRA)
Includes secure connection, User Access Control, and other advanced features.
Designed for part picking in any environment
Computing part pose (X, Y, Rz) on different structures, colors, or surfaces can be complicated—especially when high flexibility is required. EYE+ XTD was specifically developed to overcome these challenges.
With just a few clicks, you can detect various parts and orientations, and locate them on thermoformed trays, conveyors, or any other surface requiring precise part coordinates.
Thanks to a user-friendly recipe wizard powered by AI-based algorithms, training the system is simple and fast—just highlight a single part to teach the program how to recognize part positions on a tray or other complex backgrounds.
Getting part coordinates—and picking them—has never been this easy.
Tailor-made user experience (UX)
EYE+ XTD is designed to guide users effortlessly through the full setup journey—from initial installation and new recipe setup to robot programming. Configure the system efficiently by following the three main steps shown on the EYE+ XTD web interface homepage:
- Camera configuration
- Recipe creation
- Hand-eye calibration
Once complete, simply connect your preferred robot or PLC and request part coordinates using the get_part command.
EYE+ XTD takes care of lighting, image acquisition, processing, and localization—returning precise, pickable part positions directly in the robot’s coordinate system.
Try the free EYE+ XTD simulation and enjoy its simplicity
Discover the intuitive EYE+ XTD experience with a selection of predefined parts. Without any machine vision expertise, you can train the system to localize parts on trays or conveyors in just a few minutes. Simply follow the step-by-step wizard.
Sign up for a free session.
Why choose EYE+ XTD?
EYE+ XTD offers a user experience similar to the EYE+ for Asycube, enabling you to handle extended feeding applications. EYE+ XTD Studio delivers simplicity and efficiency in a ready-to-use solution dedicated to part picking.
- ONE STOP SHOP
Benefit from the same intuitive interface and high performance as EYE+, with capabilities beyond Asycube flexible feeders
- SIMPLICITY
No vision expertise required—certified by our customers - FLEXIBILITY
Teach a new part in under 15 minutes. Load new recipes within seconds
- MULTI-MODEL
Detect and pick multiple parts in different orientations using a single recipe
- SCALABILITY
Detect parts of any shape on any surface with an FOV up to 1 m²
- COMPATIBILITY
Compatible with all TCP/IP devices; just three commands needed to manage production workflow
Why choose EYE+ XTD?
EYE+ XTD offers a user experience similar to the EYE+ for Asycube, enabling you to handle extended feeding applications. EYE+ XTD Studio delivers simplicity and efficiency in a ready-to-use solution dedicated to part picking.
- ONE STOP SHOP
Benefit from the same intuitive interface and high performance as EYE+, with capabilities beyond Asycube flexible feeders
- SIMPLICITY
No vision expertise required—certified by our customers - FLEXIBILITY
Teach a new part in under 15 minutes. Load new recipes within seconds
- MULTI-MODEL
Detect and pick multiple parts in different orientations using a single recipe
- SCALABILITY
Detect parts of any shape on any surface with an FOV up to 1 m²
- COMPATIBILITY
Compatible with all TCP/IP devices; just three commands needed to manage production workflow
EYE+ XTD consists of a compact controller, a high resolution camera, and a power cable.
This system enables reliable part detection across various surfaces and devices.
EYE+ XTD
EYE+ XTD consists of a compact controller, a high resolution camera, and a power cable. This system enables reliable part localization across various surfaces and devices.
Technical description
EYE+ XTD controller
Dimensions: 141 x 187 x 71 mm
Weight: 1.26 kg
Operating temperature: +5 °C to 40 °C
Power:
Supply voltage: 24 VDC (+/- 5%)
Current: 6.5 A max
EYE+ camera
High resolution (6.3 MP)
Connectivity
4x Gigabit Ethernet (PoE for the camera)
Additional cables
PoE cable for EYE+ camera, and Ethernet cables for PLC or robot and laptop
Compatible accessories
Different frontlight colors and polarized option
External lighting supported via GPIO connector
Bandpass or polarized filters
Asycube calibration platform
Fieldbus compatibility - EtherCAT
Fieldbus compatibility - EtherNet/IP
Fieldbus compatibility - PROFINET
Technical documentation
Documentation
3D / CAD
Products details
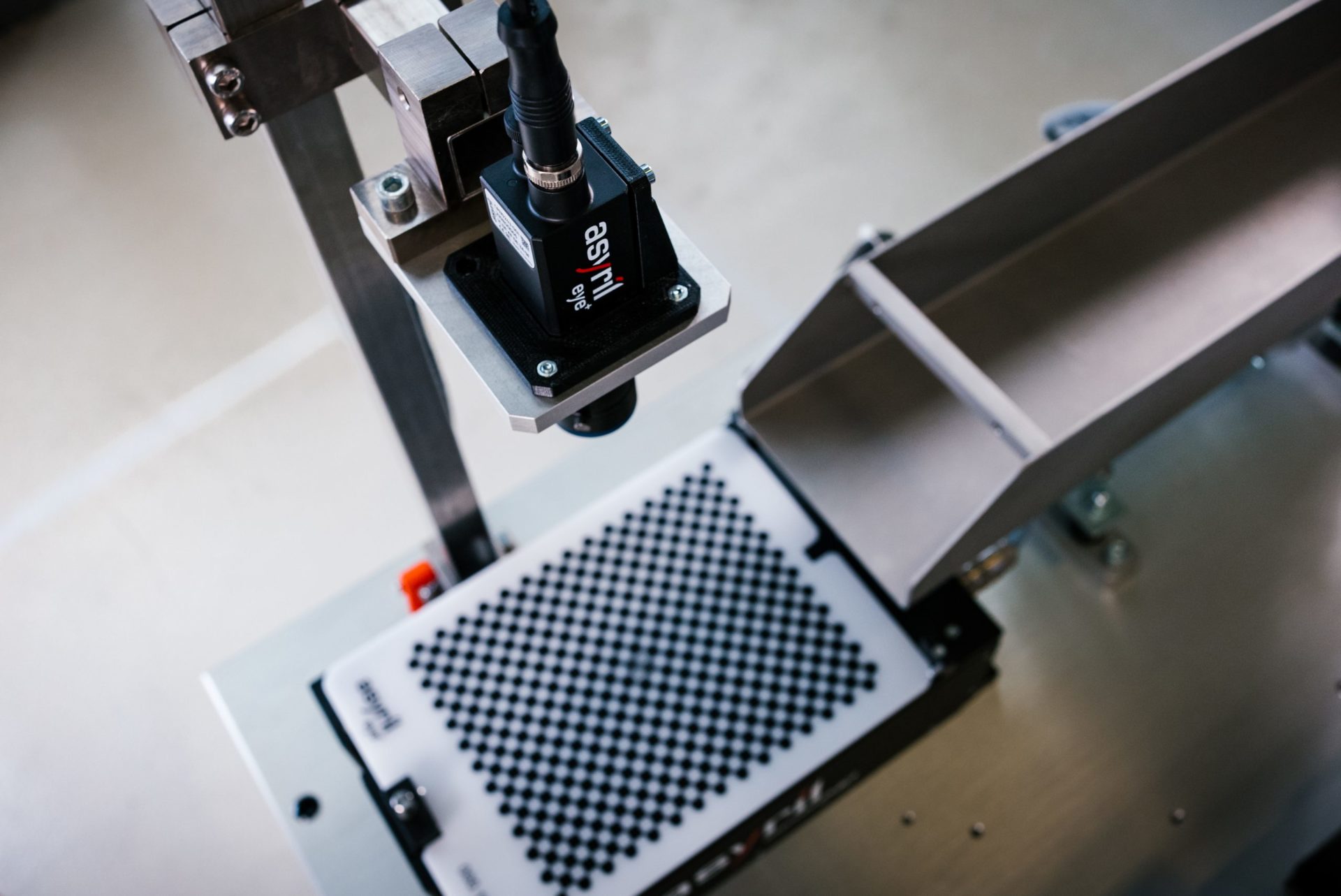
EYE+ smart control system
Solution to simplify and facilitate the integration and use of the Asyfill smart hopper and the Asycube flexible feeder while optimizing its efficiency.

Asycube flexible feeder
Complete range and patented technology for a flexible and efficient solution.
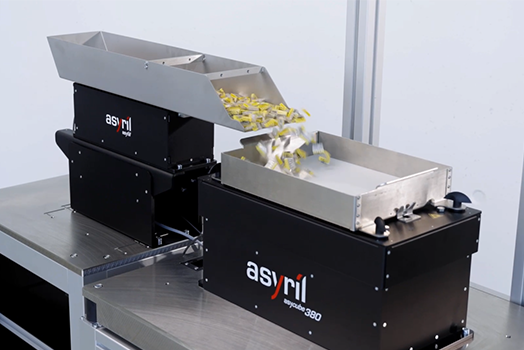